Rammed earth is often celebrated as a low-carbon method of constructing buildings, but some experts are beginning to cast doubt on its sustainability credentials. Amy Peacock reports.
“People are using rammed earth to sell something that is essentially concrete,” said Rowland Keable, CEO of the charity Earth Building UK and Ireland and founder of Rammed Earth Consulting.
“I’ve seen, in the UK, rammed-earth projects going into the glossy architecture mags and you think, ‘wow, that’s a beautiful looking building’,” added Tim Coleridge, MSc Sustainability and Adaptation programmes leader at the Centre for Alternative Technology (CAT).
“But [we’re] not talking about the cement that’s gone into making that possible.”
Rammed earth is a building method where soil, made up of a combination of aggregate, sand, silt, clay and gravel, is packed into formwork and compressed, leaving a solid wall when the formwork is removed.
Sometimes it is constructed in its raw form, but often it is stabilised with a binder, such as cement, to improve its strength and durability.
The ratio of cement in rammed-earth construction varies, but some experts claim it can be comparable to the amounts used in concrete, which is widely considered to be one of the most environmentally harmful building materials.
Cement-stabilised rammed earth comparable to concrete
Concrete is made by mixing aggregate with cement, and it’s the highly energy-intensive production of cement that generates large amounts of CO2.
“As soon as you’re using cement in ratios of five or 10 per cent in rammed earth, environmentally it’s not that much better than using a concrete block,” said Coleridge.
“It doesn’t seem like a lot, but it is a similar cement proportion to a standard concrete block, so the environmental impact of your low-impact local material has gone from being very small up to being almost on a par with the conventional, mass-produced concrete block,” he told Dezeen.
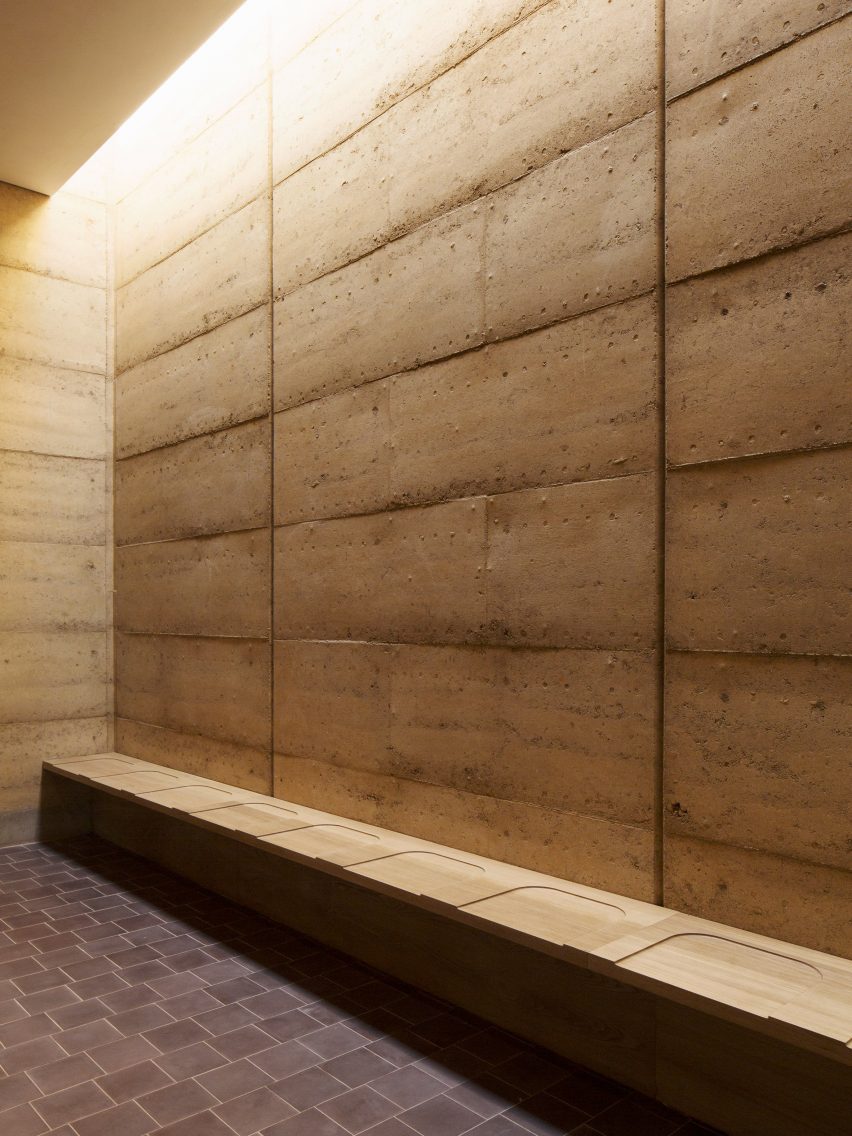
Keable echoed these concerns, adding that he believes once cement is added to soil, it should no longer be considered an earth construction material.
“Talk to an organic farmer and they’ll say, ‘we’d love to spray all of this stuff with things that kill all the little bugs eating our crops, but then we wouldn’t be organic and that’s our USP’,” he said.
“Until there’s a sense of a popular consciousness about this, then I’m always going to have a chip on my shoulder.”
James Souter, a director at British engineering firm Elliot Wood, has used cement-stabilised rammed earth in some of the projects he has worked on, including Bushey Cemetery in London.
A raw, rammed-earth wall in the UK would usually need a large overhanging roof to protect it from rain erosion, but at Bushey Cemetery, the cement content meant monolithic walls with the textured, patterned surface of rammed earth were achieved.
“It’s an aesthetic decision”
“First and foremost, it’s an aesthetic decision,” said Souter. “The best way to enhance the characteristics of rammed earth is to stabilise it with cement.”
For Souter, the concerns around cement content in rammed earth are negligible compared to the amount of concrete being produced in the UK.
“If you make a 0.1 per cent improvement to concrete mix across all the projects that are getting built from concrete in the country, it will make more of a difference than if rammed earth went from something that was comparable to other materials to this magical material that didn’t cost any carbon,” he said.
“The amount of rammed earth that actually gets used in this country is insignificant, so it’s not going to make any difference whether it’s a 3.5 per cent cement ratio or a six per cent cement ratio. The volume is so tiny it’s not even rearranging the deck chairs on the Titanic.”
It is technically possible to build modern rammed-earth buildings in the UK without stabilising the material. Coleridge highlighted the visitor centre at the Eden Project, by Grimshaw Architects, and the WISE Building at CAT in Wales, a seven-metre-tall drum-shaped unstabilised rammed-earth structure built from soil sourced from a quarry around 50 miles away.
“It’s an amazing sustainable material,” he said. “At the end of the life of the WISE Building, you can rewet the material with a hose and it will stump into a heap.”
“You could remix it and use that for another rammed earth building or it’s completely benign, you can just literally return it to the soil.”
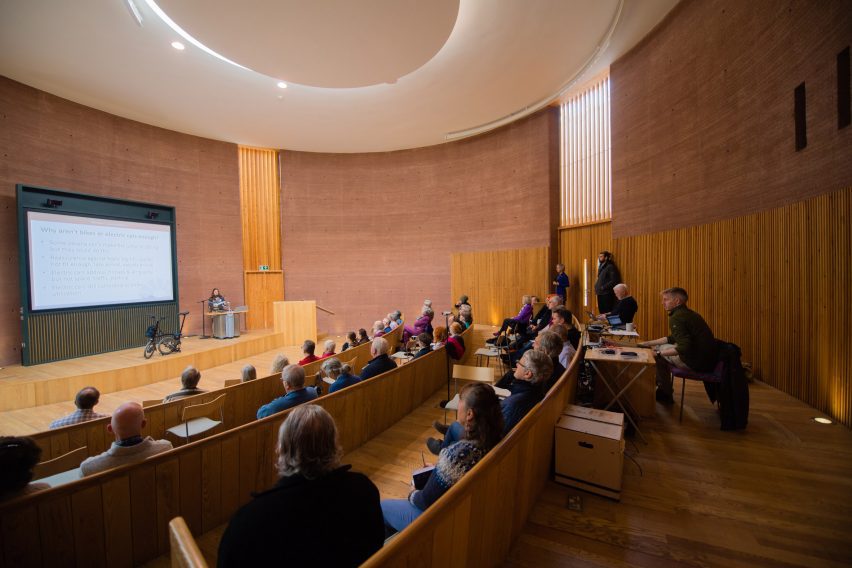
However, while ramming earth into solid building elements is an ancient construction method that is now made easier with modern machinery, it is still labour-intensive compared to other building methods.
In addition, many countries, including the UK, do not have building standards for rammed earth construction – so cement is often added to placate building control and insurers.
“Rammed earth and all the earth-building techniques are really old but they’ve been left on the shelf,” said Keable.
“Codes have been built up for concrete and other materials so with rammed earth there’s quite a bit of catching up to do,” he continued. “It’s a bit wild west and we actually need to find a point of control.”
“Lack of understanding” about rammed earth
“There’s no standard details so building with rammed earth requires a lot of bespoke work, which often comes with extra challenges around building control, insurances, even lending if you’ve got to get a mortgage on the property,” added Arup sustainable development expert Sean Lockie.
“Insurers and mortgage providers often have a very narrow view on what they’re prepared to insure and lend on.”
Coleridge explained that where there are no rammed earth standards to refer to, architects often have to use building codes for similar materials instead, including concrete.
Building codes and standards for earth construction would help popularise the material in its unstabilised form and increase awareness of its characteristics, he argued.
“If there isn’t a local code for building with earth, then designers have to defer to something else, like standards for masonry or concrete,” Coleridge said. “They might find that they’re forced to put in five or even 10 per cent cement just to satisfy insurance companies or local authorities, treating it like a concrete masonry material to get it signed off.”
“People are using cement in earth because of a lack of understanding or concern about the performance of the material,” Coleridge continued.
“It’s not going to be suitable for every situation. Having earth building codes is an enabler to building confidence and allowing local building-control departments to have an understanding of the performance of the material.”
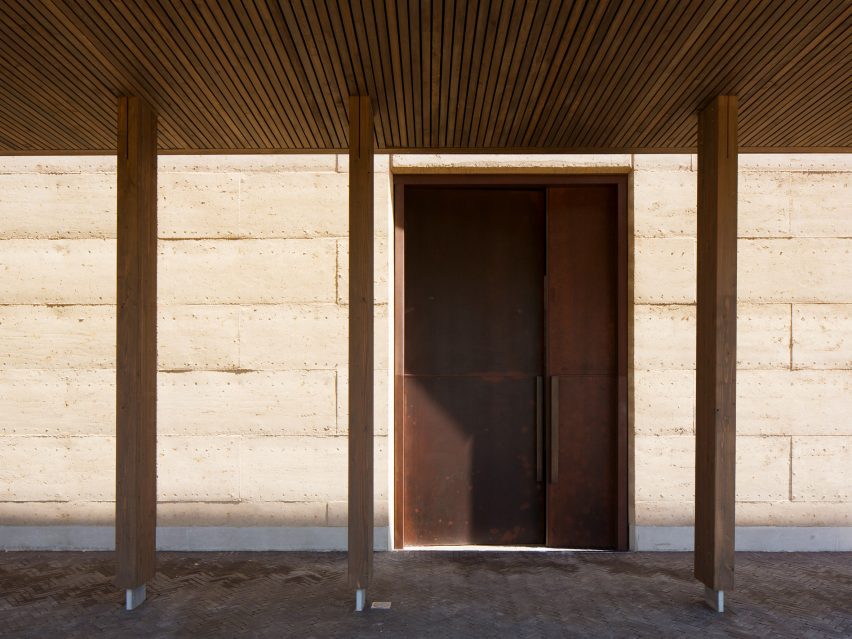
In the late 1980s, Keable began setting out building standards for rammed-earth construction in countries across Africa, which were later adopted as national standards. This included guidelines for wall thicknesses, material compaction, formwork and the mix of materials.
“By 2012, there were 15 countries with a national standard for rammed earth and by 2016 it covered the whole continent,” he said.
He has published similar guidelines in the UK that have not yet been accepted as the national standard, but Keable hopes that this can be achieved with more industry backing for rammed earth.
“A big issue across construction is that all of the materials that we know are problematic are very well funded, and all of the ones that are waiting in the wings to find wider acceptance have very little funding,” he said.
“We just don’t have the workmanship experience”
Alternative stabilisers to cement can be mixed with earth to improve its performance. Lime is a common alternative, and cob construction involves adding fibrous natural material, such as straw or horsehair, to increase tensile strength.
There are also mass-produced earth building blocks that aim to make the sustainable, natural material less labour-intensive to build with.
However, rammed earth has yet to emerge as a popular choice among architects, and few contractors in the UK have experience of working with it.
“If you compare rammed earth to things like timber, hemp brick and mycelium, a lot of these materials are starting to think about how they can be made and distributed at a large scale with modern methods of construction,” said Lockie.
“At Arup, we see it as an emerging material, but it’s going to be up against whole issues, like its ability to scale, who’s investing in its availability, what do the insurers think of it, what’s the maturity of the contracting entity – there’s not too many contractors that are that well versed in the use of it,” he continued.
“Rammed earth is more complicated to get right than, for example, exposed concrete because the experience in the industry is not there,” agreed Souter. “We just don’t have the workmanship experience in this country.”
The photography is by Lewis Khan unless otherwise stated.
Dezeen In Depth
If you enjoy reading Dezeen’s interviews, opinions and features, subscribe to Dezeen In Depth. Sent on the last Friday of each month, this newsletter provides a single place to read about the design and architecture stories behind the headlines.